Unique Continuous Taylor Flow Reactor Technology for Battery Material Development and Production
We provide patented Continuous Taylor Flow Reactors that produce high-purity, uniform substances using Taylor Fluid Flow. Manufactured by Laminar, LCTR® technology is trusted by leading organisations worldwide and offers unique benefits for battery development and production, including scalability from lab-scale research to high output commercial production.
What is LCTR® Technology?
Laminar Continuous Flow Reactors (LCTRs) use a jacketed cylindrical vessel with a central, rotating agitation bar to produce Taylor-Couette Flow (or Taylor Fluid Flow) mixing along the length of the vessel. Reagents are pumped at a controlled rate into the vessel and the reaction efficiency is maximised through specific Taylor Vortex mixing before the products are collected at the end of the vessel.
Find out more about LCTR® technology for battery development and production below; call us on +44(0)1954 232 776 or email info@analytik.co.uk to discuss your requirements with a specialist.
This video shows Cobalt Hydroxide crystallisation and demonstrates Taylor-Couette mixing visually. The well-mixed Pink solution is at the target of >pH12 and is steadily replacing the undesired blue solution (<pH12). After 30 minutes residence time, the whole vessel is Pink/well mixed and particles generated are smaller and with significantly improved uniformity compared with a conventional batch process.
The Benefits of LCTR® Technology for Battery Material Development and Production
Laminar® technology | Details | |
---|---|---|
Reduced Reaction Times | Yes | Significant decrease in reaction time (and residence time) compared to conventional continuous stirred tank reactors (CSTRs) therefore increased yield (200g/hour in 10L Taylor Vortex Reactor (TVR)). |
Particle Morphology | Yes | Spherical secondary particles composed of densely stacked primaries with high tap densities. |
Controlled Particle Size | Yes | Tunable with agitator rotation speed making (NMC) particles as small as 3-5 microns without compromising electrochemical performance. |
Scalable Process | Yes | Continuous process, scalable from laboratory reactors to production scale (working volume minimum 1L – max 1,000L). |
Fast Optimisation | Yes | Parameters used in small reactors are directly transferable to larger reactors giving same product quality. |
Introducing LCTR® Tera for battery research & development
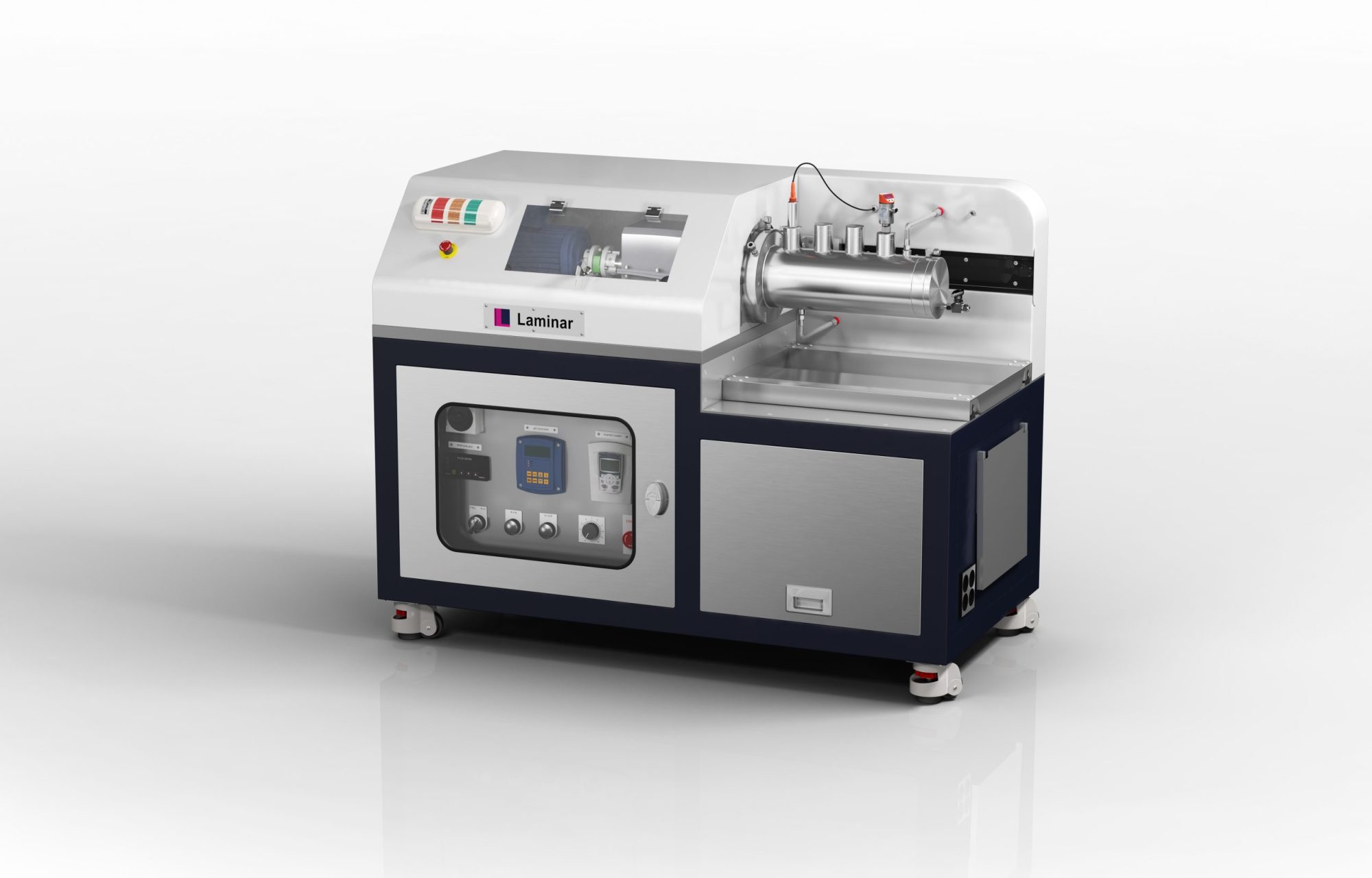
Laminar’s Tera 3100/3300 series 1 Litre reactors are ideal platforms for developing, optimising and producing various battery materials continuously at scales of up to 200g/hour. The Tera 3300 has integrated PLC control of process pumps, thermostats, simplifying operation while both variants are available with steel or Teflon coated reaction vessels.
Laminar Continuous Taylor Reactor (LCTR ®) Series – Features & Results
- Simplified operation
- Product uniformity
- Shorter residence time
Taylor Vortex Flow
- Homogeneous intense micro-mixing zone: faster reaction kinetics
- High mass and heat transfer: high degree of uniform supersaturation
- Self particle size control: high fluid shear > breakage and re-dispersion
- No dead-zone: improvement of purity, morphology, particle size & distribution, degree of crystallinity
Source: Argonne National Laboratory – Battery Materials Scale-Up and Manufacturing Research
Co-Precipitation | Lithium Battery Production | |
---|---|---|
Li – Battery | (NiMnCo)(OH)2 | |
Division | Conventional System | Laminar Reactor |
Reaction Time (h) | 10 | 3 |
Particle Size (nm) | 5-20 | 1-20 |
Span ([D90 D10]/D50) | 0.5 | 0.2 |
Tap Density (g/mL) | 2.1 | 2.2 |
- Co-Precipitation: NMC Pre-cursor
- (NiMinCo): Cathode Materials (NMC)
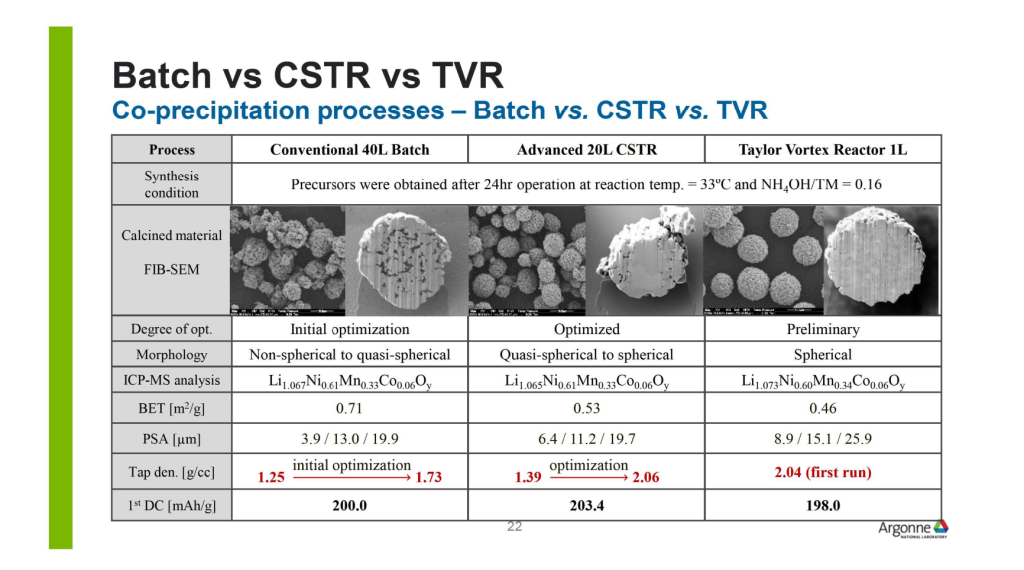
Laminar Co-precipitation Processes Based on the Chart above
Source: Argonne National Laboratory – Battery Materials Scale-Up and Manufacturing Research
The following materials have been tested and are currently in development or being produced on Laminar’s reactors:
- NMC
- NCA
- LlZO – (solid state)
- Prussian Blue / White (sodium ion battery)
- LFP
- Core-shell Particles (Nickel rich)
LCTR ® System Overview
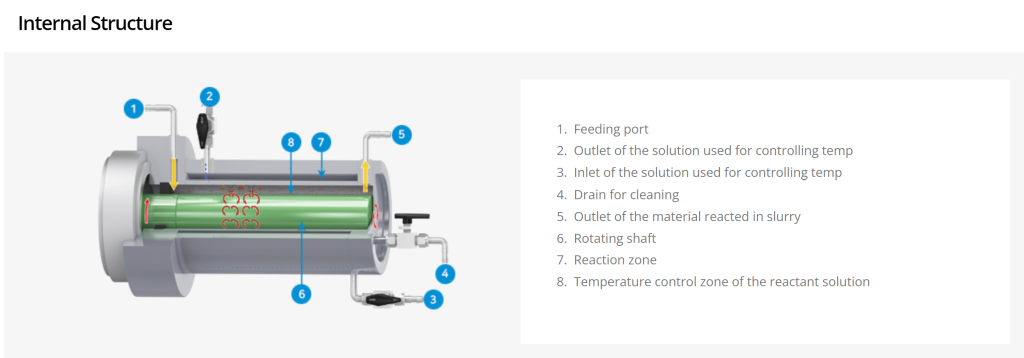
Hower on image to zoom
The development of a ideal chemical reactor. The continuous system for high purity materials by utilising the advantages of both Batch ( easy to operate, the use of mixer, easy to check in operation) and Tubular ( high purity production, high reproducibility, easy to produce nano-materials).
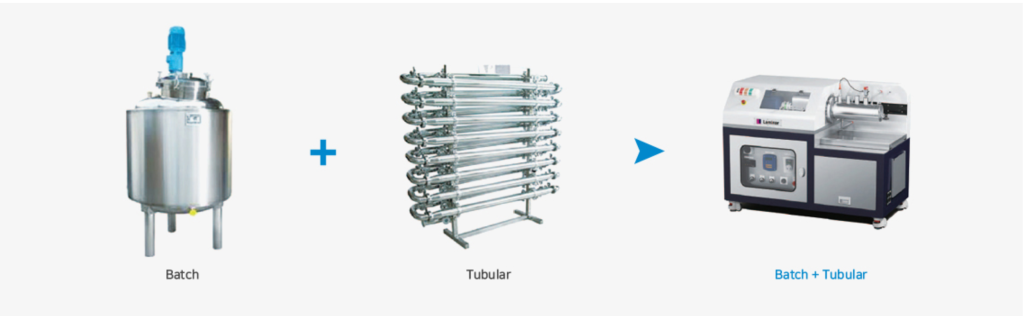
Hower on image to zoom
Continuous system in which production is controlled according to residence time.
It is possible to prepare high purity materials due to minimized dead-zones in the reactor and no gas interface.
It is possible to shorten the reaction time due to stronger mixing force and higher mass transfer velocity.
Users Around the World
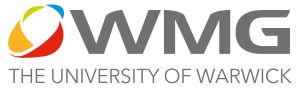
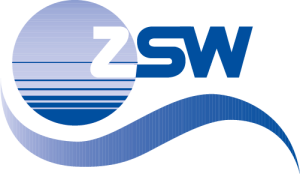
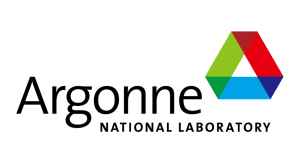
Case Study
LCTR® technology offers significant advantages compared to Conventional Continuous Stirred Tank reactors (CSTRs); these Taylor Vortex Reactors (TVRs) have reduced reaction times (and also the residence time) decreased by 3-fold which yields 3 times more of the product. For example; 200g/h in 10L TVR vs 67g/h in a 10 L CSTR.
In addition, TVRs can run processes at/above pH 12, these conditions give high tap density, spherical Ni-rich chemistry particles. pH values ≥ 12 in CSTRs pulverizes the particles which don’t form spherical morphologies and are low in density.
Particle overgrowth in CSTRs is also a problem, which the Taylor Vortex Reactor doesn’t have, in fact, you can adjust particle sizes to the desired levels by simply increasing the rotation speed. 3 – 5 µm spherical and dense particles can be successfully produced in TVRs (1L or 10L) without compromising the electrochemical performances. CSTR applications are limited to ~ 8µm, however the spherical shape and tap density of the “CSTR produced small particles” are compromised which yields distorted morphologies and low density.
Finally, optimization in TVRs is fast. In a U.S. DOE VTO funded project, the TVR delivered optimal, 12 different compositions and/or particle sizes using 1 and 10L TVRs within 1.5 years (at multiple kg quantity). When we did optimization in 1 L reactor; we transferred those exact optimal parameters, to the 10L TVR and there were no scale up issues. The same quality can be obtained in two different scales using exactly the same parameters.
Dr Ozge Kahvecioglu
Senior Materials Scientist | AMD Process R&D and Scale Up
Argonne National Laboratory
CAN’T FIND WHAT YOU’RE LOOKING FOR?
Fill out a Contact Form, call +44(0)1954 232 776 or email info@analytik.co.uk to discuss your requirements with a specialist.