High Pressure Homogenisation vs. Microfluidization
What are High Pressure Homogenisers and Microfluidizers?
‘High pressure homogeniser’ is a general term used to describe a piece of equipment that forces a stream of liquid sample through a system which applies a number of forces to ‘homogenise’ the sample, that is, to reduce the particle size of its components. There are many applications for this process – whenever an emulsion or suspension would benefit from greater efficacy, stability and downstream processing from smaller constituent particles, higher pressure homogenisation may be a valuable process solution. Microfluidizers are a form of high pressure homogeniser though work slightly differently.
A high pressure homogeniser typically uses a valve assembly to restrict flow, build pressure and subsequently force fluid through the opening valve at high velocity to apply shear forces to the liquid being processed. This relatively simple but reliable technology is widely used and highly effective in processing very large scale batches of product where a high degree of control over the particle size and distribution isn’t required.
Where Microfluidisation differs is that the shear rate applied to the liquid is higher and constant, this is achieved by using a fixed geometry microchannels rather than valves and a more sophisticated hydraulic system to apply constant pressure. This addresses the common problems of valve high pressure homogenisers and makes Microfluidizers a better choice where the top level of performance is desired, typically in high-value/advanced materials where particle size and distribution has a significant impact on the performance characteristics of the product.
Advantages and Disadvantages of a High Pressure Homogeniser
High pressure homogenisers offer some advantages over other types of homogeniser such as high shear mixers and ultra-sonication devices. Generally, the shear rates possible can be higher and the process is a continuous or pulsed flow, this means particles can be made smaller, more uniformly and scale-up is easier to achieve. In addition, a high pressure homogeniser does not leave contaminants in the product like ultrasonication, where the probe tip decays under its own cavitation forces. High shear mixers are often used in tandem with high pressure homogenisers and Microfluidizers as a valuable upstream process to create a stable coarse pre-mix before being homogenised to final specification. A high pressure homogeniser can process large volumes of liquid sample thoroughly and reproducibly and as such are a good scale-up proposition compared to ultrasonication and high-shear mixers. Process flexibility is achieved by tuning the process pressure, temperature and number of passes the sample is subjected to. With Microfluidizers, the microchannel design can be optimised by application and when scaling up, multiple parallel microchannels can support identical shear conditions at a much higher flow rate. In contrast, when scaling with high pressure homogenisers, larger valves are used, losing the original geometry and shear profile and the process must be optimised again.
It is important to consider sample size when selecting the right high pressure homogeniser or Microfluidizer for your application, the flow rate of the machine could lead to inappropriate batch processing times and machine duty cycle depending on the number of passes required for the application. In both technologies there is typically an inverse relationship between flow rate and process pressure at the highest scales; if your goal is to scale up to large volumes, consider optimising the lab scale process at a lower pressure, if possible, to give you the most options when it comes to scale up. In addition to flow rate, other benefits to this would be overall energy consumption and easier product temperature control.
Microfluidizer Processor High Pressure Homogenisers
Microfluidizer® Processor High Pressure Homogenisers are the gold standard in uniform nanoemulsions, particle size reduction and cell disruption. Microfluidisation offers many advantages over High Pressure Homogenisers including particle size and distribution performance, cooling efficiency, easy cleaning and scalability.
Microfluidizer® technology is guaranteed to scale up from lab to pilot and production volumes. Whether you are producing nanoemulsions, pursuing delicate cell disruption, creating novel suspensions or generating cutting-edge liposomes, Microfluidizer® Processor High Pressure Homogenisers is the right equipment for the job.
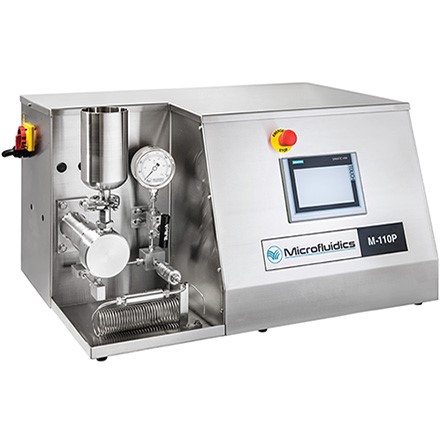