Swansea University Revolutionise Metal Powder Production with ATO Lab Plus
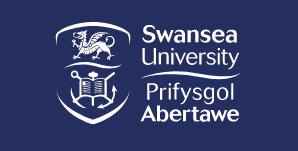
Challenge faced:
Before integrating the ATO Lab+ instrument into their alloy development workflow, the team encountered significant hurdles. External gas atomisation, their previously utilised model of developing alloys for additive manufacture, posed delays of approximately 14 weeks and mandated a minimum batch size of 200kg, creating unnecessary waste. It meant that they were unable to link their small-scale rapid alloy prototyping and in-house additive manufacturing capabilities without external powder production.
Discovering ATO Lab+
In their search for a solution, Prof Lavery’s team sought the best combination of melt temperature, powder quality and suitability for their lab environment. They found that the ATO Lab+ ultrasonic metal atomiser was well made and user-friendly, with initial showing that the machine produces quality powder with a morphology suitable for additive manufacture.
Results:
ATO Lab+ has empowered the team to overcome a major hurdle in their aim to optimise chemistries for specific applications, moving beyond legacy casting alloys commonly used in additive manufacturing. They can now swiftly produce small batches of novel compositions, for faster, more efficient production within their own lab significantly speeding up alloy discovery for a wide range of cutting-edge applications.
Looking ahead, the team plans to develop novel alloys for various additive manufacturing techniques, including LPBF, BJ, blown powder, and HIP.
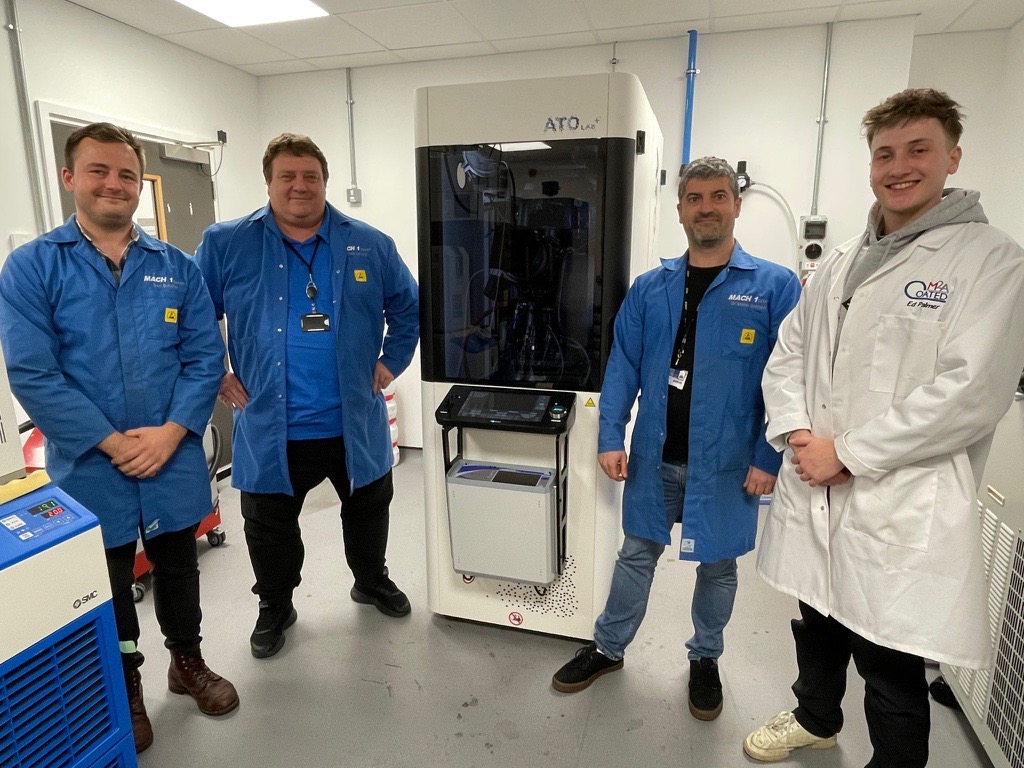
Commenting on his experience purchasing the ATO Lab+,”
Analytik are easy to deal with and Hiran was a pleasure to meet. The ATO Lab+ machine is well manufactured and 3D lab have been very helpful with all aspects including procurement, installation, commissioning, training and troubleshooting.”
Professor Nick Lavery
Swansea University